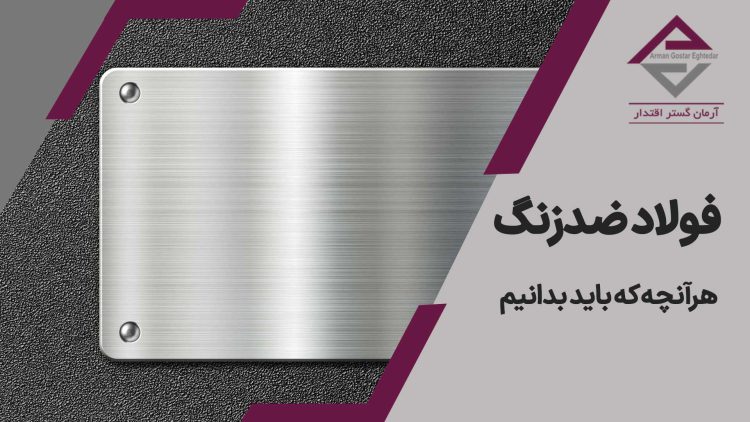
فولاد ضد زنگ: موسسه آهن و فولاد جهانی (AISI)
فولاد ضد زنگ: موسسه آهن و فولاد جهانی (AISI) فولاد ضد زنگ را به عنوان فولادی تعریف می کند که حاوی 10 درصد یا بیشتر کروم به تنهایی یا با عنصر آلیاژی دیگر باشد. کروم باعث ایجاد یک لایه نازک اکسید بر روی سطح فولاد به نام “لایه غیرفعال” می شود که به جلوگیری از خوردگی سطح کمک می کند. امروز انواع مختلفی از فولاد ضدزنگ در بازار وجود دارد که در این مقاله با آنها آشنا می شویم.
تحریریه آرمان گستر اقتدار (آهن آرمان):فولاد ضدزنگ هرآنچه که باید بدانیم. مرجع فروش و عرضه کلیه آهن آلات و مقاطع فولادی (تماس 58336-021)
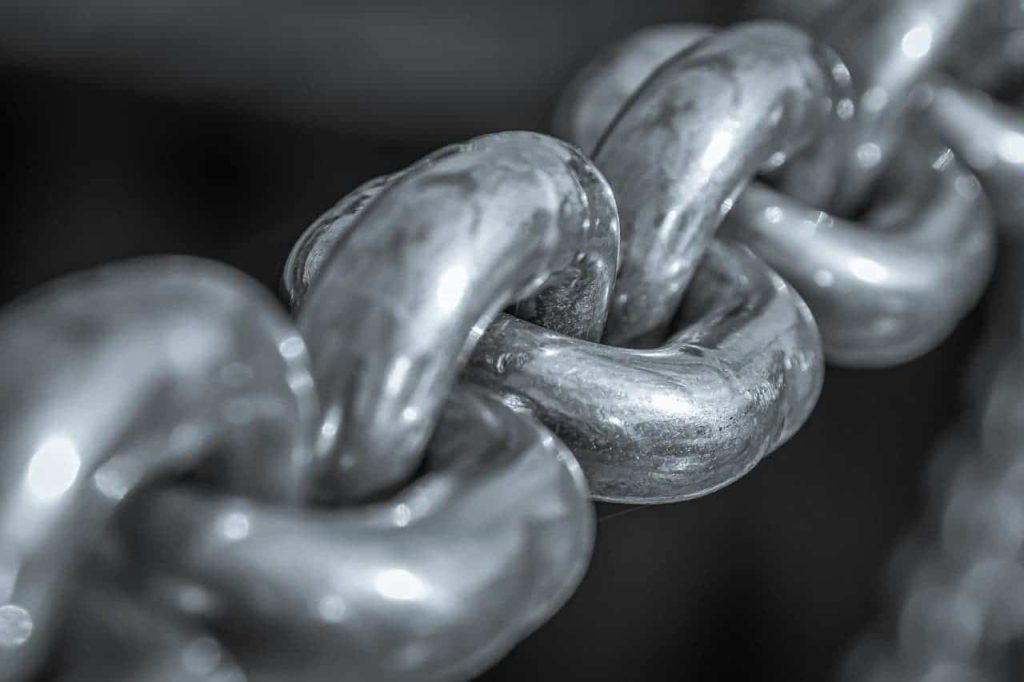
آنچه در این مقاله خواهید خواند:
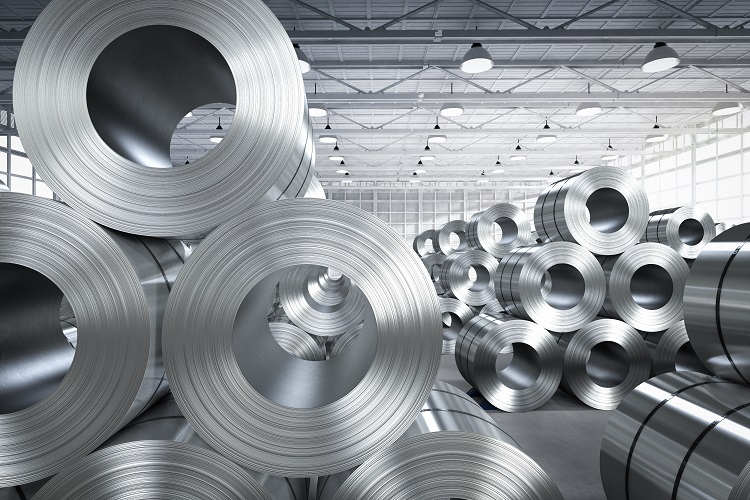
فولاد ضد زنگ
هیچ کس نمی داند چه کسی فولاد را اختراع کرد. منشأ دقیق آن در طول تاریخ بشریت گم شده است که به آهنگران اولیه در چین، هند باستان و سریلانکا و خاورمیانه و بریتانیا در طول انقلاب صنعتی نسبت داده شده است و هر کدام به نوعی در توسعه و تکثیر فولاد در سراسر جهان نقش داشته اند. با این حال، اختراع فولاد ضد زنگ، محصول سال ها آزمایش و آزمون و خطا است. فولاد ممکن است ماده فوق العاده سختی باشد اما این بدان معنا نیست که هیچ نقطه ضعفی ندارد. فولاد با افزودن کربن به آهن ساخته می شود و آهن به ناچار زنگ می زند. بزرگترین نقطه ضعف فولاد اکسیده شدن (زنگ زدن) آن است.
امروزه موسسه آهن و فولاد جهانی (AISI) فولاد ضد زنگ (Stainless Steel) را به عنوان فولادی تعریف می کند که حاوی 10 درصد یا بیشتر کروم (به تنهایی یا با عنصر آلیاژی دیگر) باشد. عنصر کروم میزان سختی، استحکام و مقاومت در برابر خوردگی را افزایش می دهد. البته عنصر نیکل نیز مزایای مشابهی دارد، اما بدون از بین بردن شکل پذیری و چکش پذیری، میزان سختی را اضافه می کند. همچنین انبساط حرارتی را برای ثبات ابعادی بهتر کاهش می دهد.
فولاد ضدزنگ توسط تولیدکنندگان برتر فولاد جهان تولید می شود. برای آشنایی با برترین فولاد سازان اینجا را کلیک بفرمایید.
شما میتوانید برای مشاوره خرید انواع مقاطع فولادی، فولاد ضد زنگ و فولاد آلیاژی برای پروژه های خود و دریافت قیمت روز با شماره 02158336، شرکت آرمان گستر اقتدار (آهن آرمان) تماس بگیرید
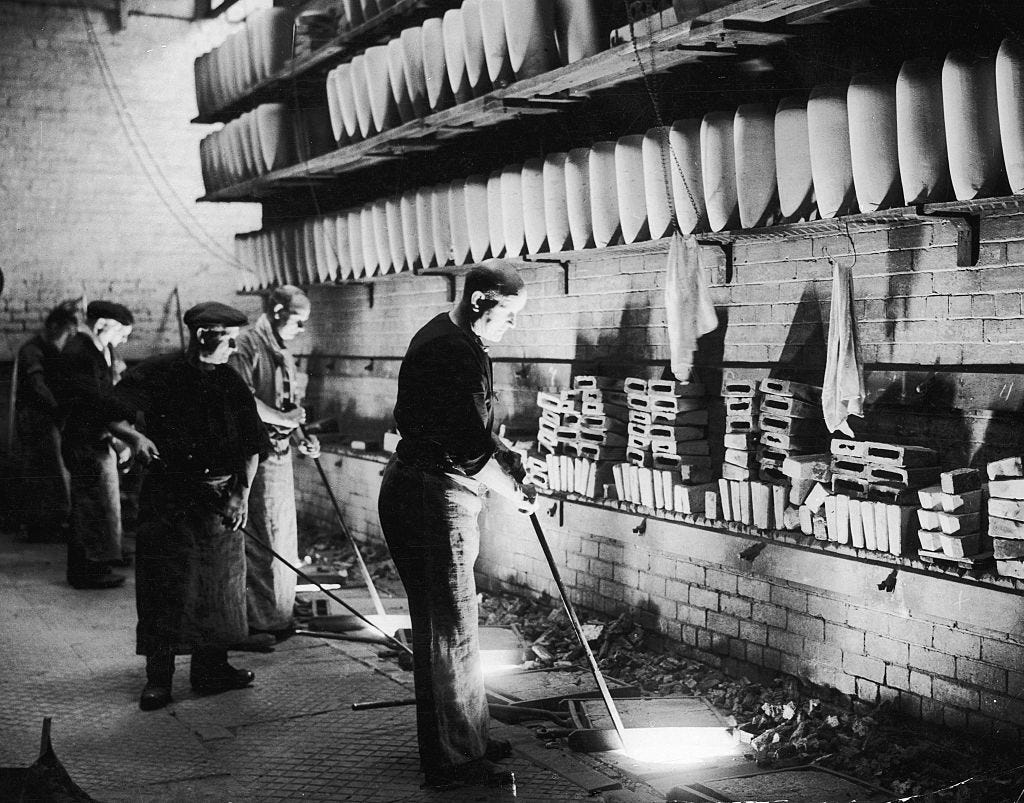
اختراع فولاد ضدزنگ
برای سالهای متمادی، متالوژیستها در سراسر جهان تلاش کردند تا بر ضعف فولاد غلبه کنند. آزمايش های متداول، معمولا افزودن عناصر ديگر به آهن بود و با موفقيت متوسط و جزئی همراه بود. اختراع فولاد ضد زنگ به دنبال یک سری پیشرفت های علمی بود که از سال 1798 شروع شد، زمانی که کروم برای اولین بار توسط لوئی واکلین Louis Vauquelin به آکادمی فرانسه نشان داده شد. در اوایل دهه 1800، دانشمندان بریتانیایی جیمز استودارت، مایکل فارادی و رابرت مالت مقاومت آلیاژهای کروم-آهن (“فولادهای کروم”) را در برابر عوامل اکسید کننده مشاهده کردند. رابرت بونسن مقاومت کروم در برابر اسیدهای قوی را کشف کرد. فولاد مقاوم در برابر خوردگی – آلیاژی از آهن و کروم – اولین بار در سال 1821 توسط پیر برتیه Pierre Berthier، متالورژیست فرانسوی، شناخته شد.
علیرغم کشف فولاد ضدزنگ در سال 1821، متالورژیست های آن زمان نتوانستند تعادلی بین درصد کروم بالا و کربن پایین که فولاد ضد زنگ مدرن را تا این حد موثر می کند، بیابند. محصولاتی که آنها تولید می کردند خاصیت ضد زنگ کمی داشتند و برای استفاده عملی بسیار شکننده بودند. در سال 1872، دو انگلیسی به نام های کلارک و وودز، آلیاژی بسیار نزدیک به معادل فولاد ضد زنگ مدرن امروزه، ترکیبی از کروم (30-35٪) و تنگستن (2٪) را ثبت اختراع کردند. با اینحال تا 40 سال بعد، تلاش ها بیهوده بود و علیرغم ثبت اختراع، بدون یافتن روش ساخت کاربردی، آلیاژ مذکور به صورت تولید انبوه برای بازار عرضه نشد.
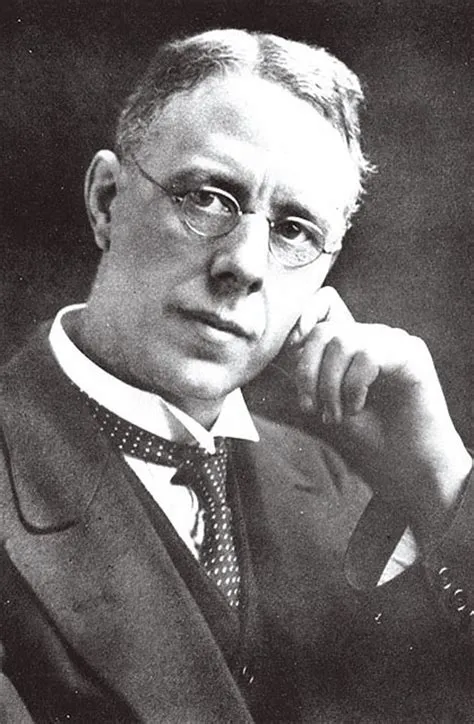
ثبت فولاد ضد زنگ
با این حال، در سال 1912 بود که یک روش قابل اعتماد برای تولید انبوه فولاد ضد زنگ کشف شد. هری بریری Harry Brearley در کارخانه تحقیقاتی براون-فرث در شهر صنعتی شفیلد انگلستان کار می کرد. او ساعتهای بیشماری را صرف جستجوی آلیاژی قوی و مناسب برای لولههای تفنگ کرد که در آن زمان به آسانی فرسوده میشدند. تلاشهای او ماهها به طول انجامید، و در حالی که انباشته ضایعات در کنار میز کارش زنگ زده بود، متوجه بشکهای شد که در میان ضایعات زنگ زده میدرخشید. این نمونه خاص تقریباً حاوی 12.8٪ کروم و 0.24٪ کربن بود. در آن زمان، شفیلد به دلیل تولید کارد و چنگال های باکیفیت شناخته شده بود که معمولاً از فولاد یا نقره ساخته می شدند. فولاد به راحتی زنگ می زد و برای جلوگیری از آلودگی باید دائما تمیز می شد و نقره برای اکثر مردم بسیار گران بود.
پس او برای تولید کارد و چنگال از این آلیاژ جدید استفاده کرد. کشف او در روزنامه نیویورک تایمز (ژانویه 1915) به نام فلز “زنگ ضدزنگ، غیرقابل تغییر و بدون لکه” توصیف شد. محبوبیت این فلز بقدری بالا رفت که تا سال 1929، بیش از 25،000 تن فولاد ضد زنگ تنها در ایالات متحده تولید و فروخته شد.
جهت مطالعه روش های ساخت فولاد میتوانید به “مقاله فولاد چیست” مراجعه بفرمایید.
شما میتوانید برای مشاوره خرید انواع مقاطع فولادی، دریافت قیمت روز و اطلاع از موجودی تهران و کارخانه ها، با شماره 02158336 شرکت آرمان گستر اقتدار (آهن آرمان) تماس بگیرید تا کارشناسان ما، پاسخگوی سوالات شما باشند.
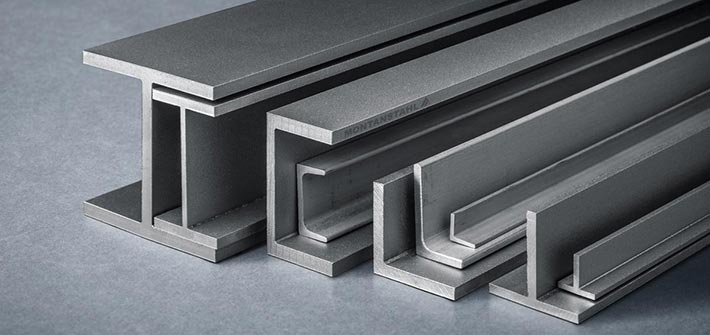
مشخصات
مقاومت فولادهای ضدزنگ (همچنین به عنوان فولاد Inox شناخته می شود) در برابر خوردگی، عدم لکه پذیری، ترمیم و نگهداری آسان آن را به یک ماده ایده آل برای بسیاری از کاربردها تبدیل می کند که در آن هم مقاومت فولاد و هم مقاومت در برابر خوردگی مورد نیاز است. فولاد ضد زنگ، آلیاژی از آهن با حداقل 10.5٪ کروم و در برخی موارد نیکل و سایر فلزات مقاوم در برابر خوردگی است. کروم به دلیل تولید یک لایه نازک اکسید بر روی سطح فولاد به نام “لایه غیرفعال” استفاده می شود که به جلوگیری از خوردگی بیشتر سطح کمک می کند و در حضور اکسیژن خود-ترمیم شود. افزایش مقاومت در برابر خوردگی را می توان با افزایش مقدار کروم به دست آورد.
مقاومت عالی در برابر زنگ زدگی به دلیل محتوای کروم است که معمولاً بین 12 تا 20 درصد کل آلیاژ را شامل می شود. عناصر دیگری مانند نیکل و مولیبدن ممکن است برای ایجاد خواص مفید دیگر مانند افزایش شکل پذیری و افزایش مقاومت در برابر خوردگی اضافه شوند. خواص آلیاژ نهایی با تغییر مقادیر این عناصر تنظیم می شود. به عنوان مثال، گنجاندن نیتروژن در آلیاژ به بهبود خواص کششی مانند شکلپذیری و مقاومت در برابر خوردگی کمک میکند، که آن را برای استفاده در فولادهای ضد زنگ دوبلکس مفید میکند. بنابراین، درجات متعددی از فولاد ضد زنگ با محتوای متفاوت متفاوت برای محیط های کاری مختلف وجود دارد.
فولاد ضد زنگ کاملاً قابل بازیافت و بینهایت “مواد سبز” بینظیر است. علاوه بر این، ترکیباتی را که می توانند ترکیب آن را در تماس با عناصری مانند آب تغییر دهند، شستشو نمی دهد. مزایای زیست محیطی، فولاد ضد زنگ از نظر زیبایی نیز جذاب، بسیار بهداشتی، با امکان نگهداری آسان و بسیار بادوام است که کاربردهای مختلفی را ارائه می دهد.
فولاد ضد زنگ را می توان به صورت ورق، صفحات، میله، سیم و لوله نورد کرد که می توان در ظروف آشپزی، کارد و چنگال، ابزار جراحی، لوازم اصلی، وسایل نقلیه، مصالح ساختمانی در ساختمان های بزرگ، تجهیزات صنعتی (به عنوان مثال در کارخانه های کاغذسازی، کارخانه های شیمیایی، تصفیه آب) و مخازن و تانکرهای ذخیره سازی مواد شیمیایی و محصولات غذایی استفاده کرد. تمیزی بیولوژیکی فولاد ضد زنگ نسبت به آلومینیوم و مس برتر است و با شیشه قابل مقایسه است. تمیزی، استحکام و مقاومت در برابر خوردگی آن باعث استفاده از فولاد ضد زنگ حتی در کارخانه های دارویی و مواد غذایی شده است.
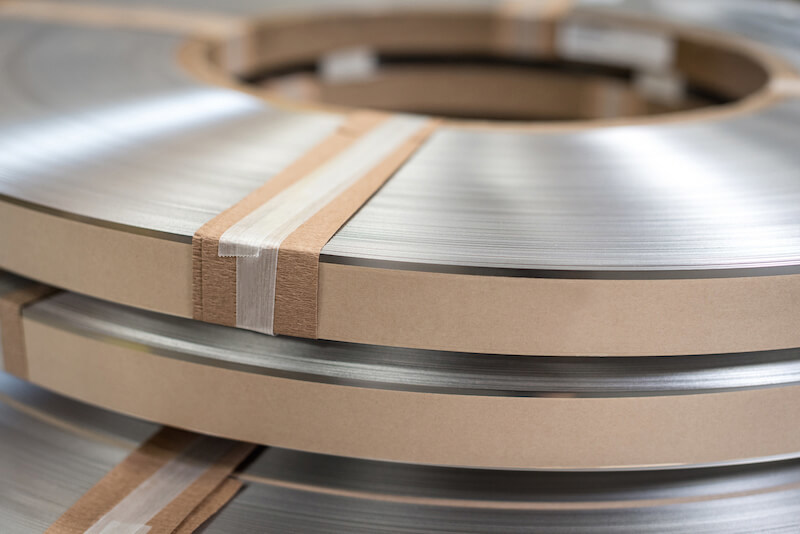
ویژگی ها
زیبایی شناسی: فولاد ضد زنگ دارای تنوع زیادی از پوشش های سطحی، از مات تا روشن، جمله برس خورده Brushed و یا حکاکی شده است. می توان آن را برجسته یا رنگ آمیزی کرد که آن را به یک ماده منحصر به فرد و زیبا تبدیل می کند. از این ماده اغلب توسط معماران برای بخش های مختلفی بیرونی ساختمان، طراحی داخلی و طراحی فضای عمومی (در معرض رطوبت) استفاده می شود.
ویژگی های مکانیکی: در مقایسه با سایر مواد، فولاد ضد زنگ دارای خواص مکانیکی قوی در دمای محیط است چون هر که باشد پایه این ماده، فولاد است! به طور خاص، شکلپذیری، کشش و سختی را با هم ترکیب میکند و آن را قادر میسازد تا در حالتهای سخت شکلدهی فلز (کوبش عمیق، خمش صاف، اکستروژن و غیره) استفاده شود و در عین حال مقاومت عالی در برابر سایش سنگین (اصطکاک، ضربه، کشیده شدن و غیره) و عکس العمل خوبی در دماهای پایین و بالا را ارائه می دهد.
مقاومت در برابر آتش: فولاد ضد زنگ بهترین مقاومت در برابر آتش را در بین تمام مواد فلزی هنگام استفاده در کاربردهای ساختاری دارد و دمای بحرانی آن بالای 800 درجه سانتیگراد است. فولاد ضد زنگ برای مقاومت در برابر آتش و بدون انتشار دود سمی در رتبه A2s1d0 قرار دارد.
مقاومت در برابر خوردگی: فولاد ضد زنگ با حداقل محتوای کروم 10.5 درصد به طور مداوم توسط یک لایه غیرفعال اکسید کروم محافظت می شود که به طور طبیعی بر روی سطح از طریق واکنش کروم با اکسیژن هوا یا آب تشکیل می شود. اگر سطح خراشیده شود، خود را بازسازی می کند. این ویژگی به فولادهای ضد زنگ مقاومت در برابر خوردگی آنها را می دهد.
قابلیت تمیز شدن: اقلام فولادی ضد زنگ به راحتی تمیز می شوند، محصولات تمیز کننده معمولی (مواد شوینده، پودر صابون) کافی هستند و به سطح آسیب نمی رسانند. فولاد ضد زنگ به طور کامل الزامات دکوراسیون و ظروف پخت و پز را که نیاز به شستشوی مکرر و موثر دارند برآورده می کند.
بازیافت: فولاد ضد زنگ جزء دسته بندی “مواد سبز” است و بی نهایت قابل بازیافت است. در بخش ساخت و ساز، نرخ بازیابی واقعی آن نزدیک به 100٪ است. در هنگام تماس با عناصری مانند آب از نظر محیطی خنثی و بی اثر است و ترکیباتی را که ممکن است ترکیب آنها را تغییر دهند از بین نمی برد. این ویژگیها باعث میشود که فولاد ضد زنگ برای کاربردهای ساختمانی که در معرض آب و هوای نامساعد قرار دارند، مانند سقفها، نماها، سیستمهای بازیابی آب باران و لولههای آب خانگی مناسب باشد. طول عمر فولاد ضد زنگ الزامات ساخت و ساز پایدار را برآورده می کند و نصب موثر، نصب و نگهداری کم، عمر مفید بی نظیری را برای کاربر تضمین می کند.
دسته بندی های اصلی
بیش از 150 گرید فولاد ضد زنگ وجود دارد که 15 مورد از آنها بیشتر استفاده می شود. چندین سیستم برای درجه بندی فولادهای ضد زنگ و سایر فولادها از جمله گریدهای فولاد SAE ایالات متحده وجود دارد. سیستم شماره گذاری یکپارچه برای فلزات و آلیاژها (UNS) توسط ASTM در سال 1970 ایجاد شد. اروپایی ها EN 10088 را برای همین هدف توسعه داده اند. برای فولاد ضدزنگ، پنج خانواده اصلی وجود دارد که بر اساس ساختار کریستالی خود طبقه بندی می شوند :
- فولادهای زنگ نزن آستنیتی (سری 200 و 300)
- فولادهای ضد زنگ فریتی (سری 400)
- فولادهای ضد زنگ مارتنزیتی (سری 400 و 500)
- فولادهای ضد زنگ رسوب سخت (PH)
- آلیاژهای دوبلکس/فولاد ضد زنگ
Austenitic: فولادهای ضدزنگ آستنیتی (سری 200 و 300)
فولادهای زنگ نزن آستنیتی رایج ترین و بزرگترین خانواده فولادهای زنگ نزن با حداقل 16 درصد کروم هستند که حدود دو سوم کل تولید فولاد ضد زنگ را تشکیل می دهند و دارای بهترین مقاومت در برابر خوردگی هستند. آنها حاوی یک ریزساختار آستنیتی هستند که یک ساختار کریستالی مکعبی محور است (مکعب بدن-محور نوعی آرایش اتمی طبیعی بصورت مکعب های همجوار و مرتب شده است که در هر گوشه هر مکعب یک اتم مشترک با مکب مجاور قرار گرفته و یک اتم نیز در مرکز آن قرار دارد). ریزساختار آنها از افزودن نیکل، منگنز و نیتروژن به دست می آید. نقطه ضعف آنها این است که نمی توان با عملیات حرارتی آنها را سخت کرد زیرا در همه دماها دارای ساختار یکسانی هستند. در مقابل ریزساختار آستنیتی به آنها شکل پذیری و جوش پذیری عالی را به آنها می دهد. فولادهای زنگ نزن آستنیتی را می توان به دو زیر گروه سری 200 و سری 300 تقسیم کرد:
- سری 200 شامل آلیاژهای کروم و منگنز و نیکل هستند که با استفاده از افزودن عناصر منگنز و نیتروژن، استفاده از عنصر نیکل به حداکثر میرسانند. سری 200 به دلیل افزودن نیتروژن دارای 50٪ استحکام تسلیم بالاتری نسبت به فولاد ضد زنگ سری 300 است. به عنوان مثال: نوع 201 از طریق سرما و برودت قابل سخت شدن است. نوع 202 یک فولاد ضد زنگ همه منظوره است. با کاهش مقدار نیکل و افزایش محتوای منگنز، مقاومت به خوردگی کاهش می یابد.
- سری 300 آلیاژهای کروم نیکل هستند و ریزساختار منحصراً با آلیاژ نیکل به دست میآیند. این سری پرکاربردترین و بزرگترین گروه است. بهترین گرید شناخته شده نوع 304 است که به ترتیب به دلیل ترکیب 18 درصد کروم و 8 درصد از 10 درصد نیکل به 18/8 و 18/10 نیز معروف است. دومین فولاد زنگ نزن آستنیتی معمولی نوع 316 است. افزودن 2% مولیبدن مقاومت بیشتری در برابر اسیدها و خوردگی موضعی ناشی از یون های کلرید ایجاد می کند.
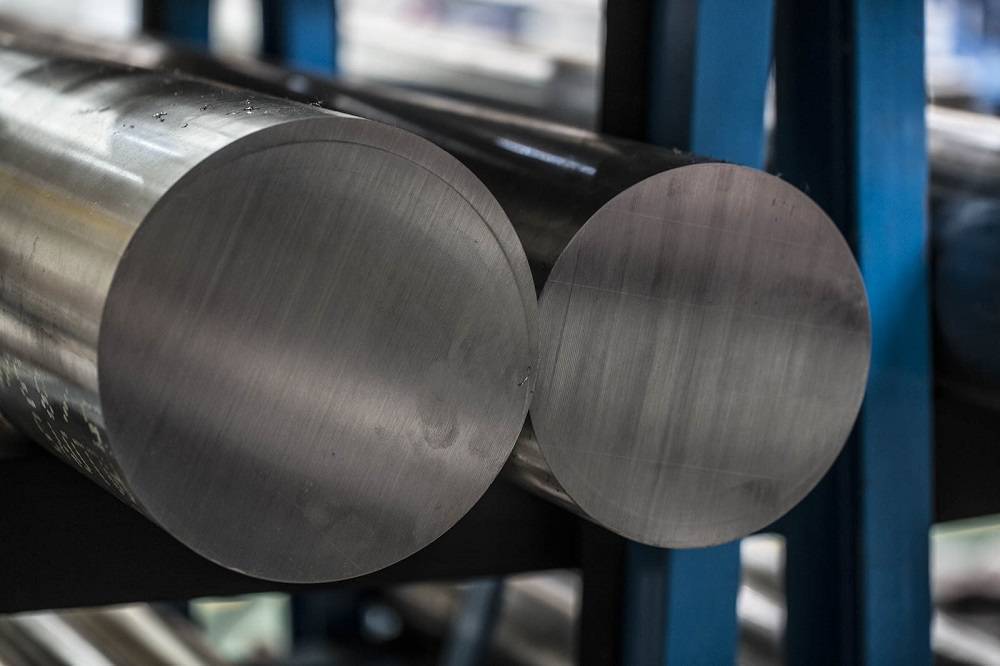
Ferritic: فولادهای ضد زنگ فریتی (سری 400)
فولادهای ضدزنگ فریتی دارای ریزساختار فریتی مانند فولاد کربنی هستند که یک ساختار کریستالی مکعبی بدنه است و حاوی بین 10.5 تا 27 درصد کروم با نیکل بسیار کم یا بدون نیکل است. چون این ریزساختار به دلیل افزودن کروم در تمام دماها وجود دارد، بنابراین با عملیات حرارتی قابل سخت شدن نیستند. آنها را نمی توان با کار سرد به اندازه فولادهای زنگ نزن آستنیتی تقویت کرد. در عوض آنها مغناطیسی هستند. افزودن نیوبیم (Nb)، تیتانیوم (Ti) و زیرکنیوم (Zr) به نوع 430 امکان جوش پذیری خوبی را فراهم می کند. به دلیل تقریباً عدم وجود نیکل، قیمت کمتری نسبت به فولادهای آستنیتی دارند و در بسیاری از محصولات وجود دارند که عبارتند از:
- لوله های اگزوز خودرو (نوع 409 و 409 Cb[b] در آمریکای شمالی استفاده می شود؛ گریدهای تثبیت شده نوع 439 و 441 در اروپا استفاده می شود)
- کاربردهای معماری و سازه (نوع 430 که حاوی 17 درصد کروم است)
- اجزای ساختمان، مانند قلاب های تخته سنگی، سقف ها، و کانال های دودکش
- Power plates در سلول های سوختی اکسید جامد که در دمای حدود 700 درجه سانتیگراد (1300 درجه فارنهایت) کار می کنند (فریتیک های کروم بالا حاوی 22٪ کروم)
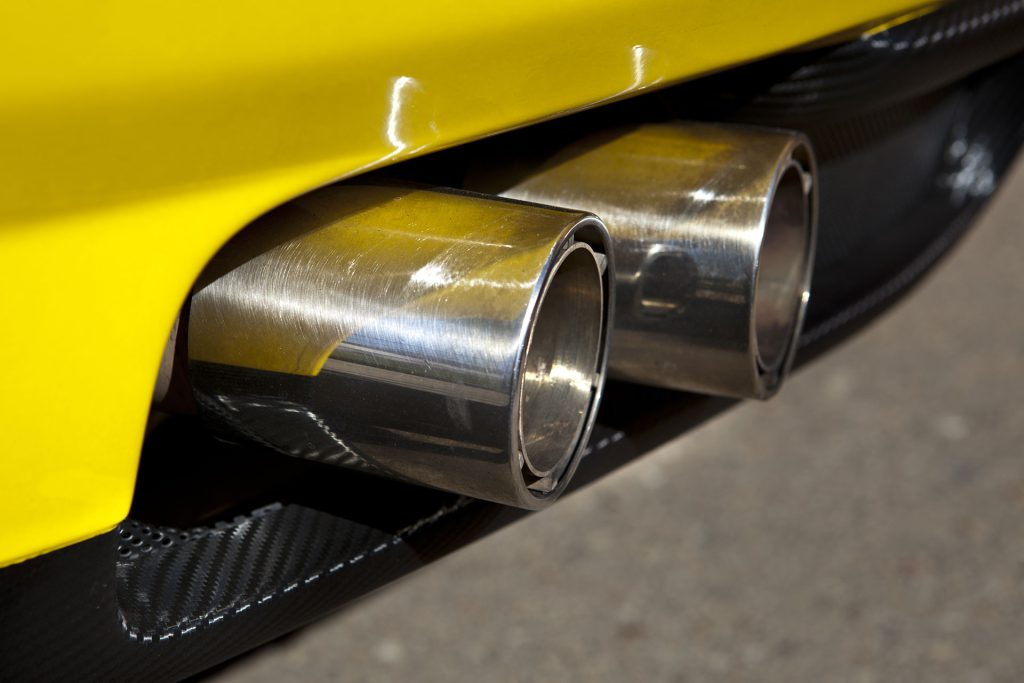
Martensitic :فولادهای ضد زنگ مارتنزیتی (سری 400 و 500)
فولادهای ضدزنگ مارتنزیتی دارای ساختار کریستالی مکعبی Body-Center هستند و طیف وسیعی از خواص را ارائه می دهند و به عنوان فولادهای مهندسی زنگ نزن، فولادهای ابزار ضد زنگ و فولادهای مقاوم در برابر تغییرشکل استفاده می شوند. فولادهای زنگ نزن مارتنزیتی (سری 400 و 500) بیشترین سختی را دارند و مغناطیسی هستند و به دلیل محتوای کم کروم آنها مانند فولادهای زنگ نزن فریتی و آستنیتی در برابر خوردگی مقاوم نیستند اما در مقابل بسیار سخت بوده و نشکن می باشند و حتی قابل سخت شدن با عملیات حرارتی نیز را دارند. آنها به چهار دسته تقسیم می شوند:
- گرید Fe-Cr-C. : این گرید اولین درجه های مورد استفاده بوده و هنوز هم به طور گسترده در مهندسی و کاربردهای مقاوم در برابر سایش استفاده می شوند.
- گرید Fe-Cr-Ni-C. : مقداری کربن با نیکل جایگزین می شود. آنها چقرمگی بالاتر و مقاومت در برابر خوردگی بالاتری را ارائه می دهند. گرید EN 1.4303 Casting Grade CA6NM با 13% کروم و 4% نیکل برای اکثر توربین های پلتون، کاپلان و فرانسیس در نیروگاه های برق آبی استفاده می شود زیرا دارای خواص ریخته گری خوب، جوش پذیری خوب و مقاومت خوب در برابر فرسایش حفره ای است.
- گرید سخت ترین: درجه EN 1.4542 که به عنوان PH 17-4 نیز شناخته می شود، معروف ترین و شناخته شده ترین گرید این دسته بندی بوده که خاصیت سخت شدن مارتنزیتی و سخت شدن بارشی را با هم ترکیب می کند. محصول نهایی به استحکام بالا و چقرمگی خوب دست می یابد و در صنعت هوا فضا استفاده می شود.
- گرید مقاوم در برابر تغییرشکل: افزودنهای کوچک نیوبیم، وانادیم، بور و کبالت استحکام و مقاومت در برابر خزش را تا حدود 650 درجه سانتیگراد (1200 درجه فارنهایت) افزایش میدهد.
- جدید: جایگزینی مقداری کربن در فولادهای زنگ نزن مارتنزیتی با نیتروژن از سال 2020 یک پیشرفت جدید است. حلالیت محدود نیتروژن با فرآیند پالایش الکتروسرباره تحت فشار (PESR) افزایش می یابد، که در آن ذوب تحت فشار نیتروژن بالا انجام می شود. فولاد بدست آمده حداکثر حاوی تا 0.4 درصد نیتروژن به است که منجر به سختی و استحکام بالاتر و مقاومت در برابر خوردگی بالاتر می شود. از آنجایی کهPESR گران است، مقادیر نیتروژن کمتر اما قابل توجهی با استفاده از فرآیند استاندارد AOD بدست آمده است.
فولادهای زنگ نزن مارتنزیتی را می توان برای ایجاد خواص مکانیکی بهتر عملیات حرارتی کرد. عملیات حرارتی معمولاً شامل سه مرحله است:
- آستنیته کردن: که در آن فولاد تا دمایی در محدوده 980-1050 درجه سانتیگراد بسته به درجه حرارت داده می شود. آستنیت به دست آمده دارای ساختار کریستالی مکعبی است.
- خاموش کردن: آستنیت به مارتنزیت یک ساختار کریستالی چهارضلعی تبدیل می شود. مارتنزیت کوئنچ شده برای اکثر کاربردها بسیار سخت و شکننده است. البته ممکن است مقداری آستنیت باقیمانده باقی بماند.
- معتدل کردن: مارتنزیت تا حدود 500 درجه سانتیگراد گرم می شود، در دما نگهداری می شود و سپس با هوا خنک می شود. دماهای بالاتر استحکام تسلیم و استحکام کششی نهایی را کاهش میدهد اما ازدیاد طول و مقاومت در برابر ضربه را افزایش میدهد.
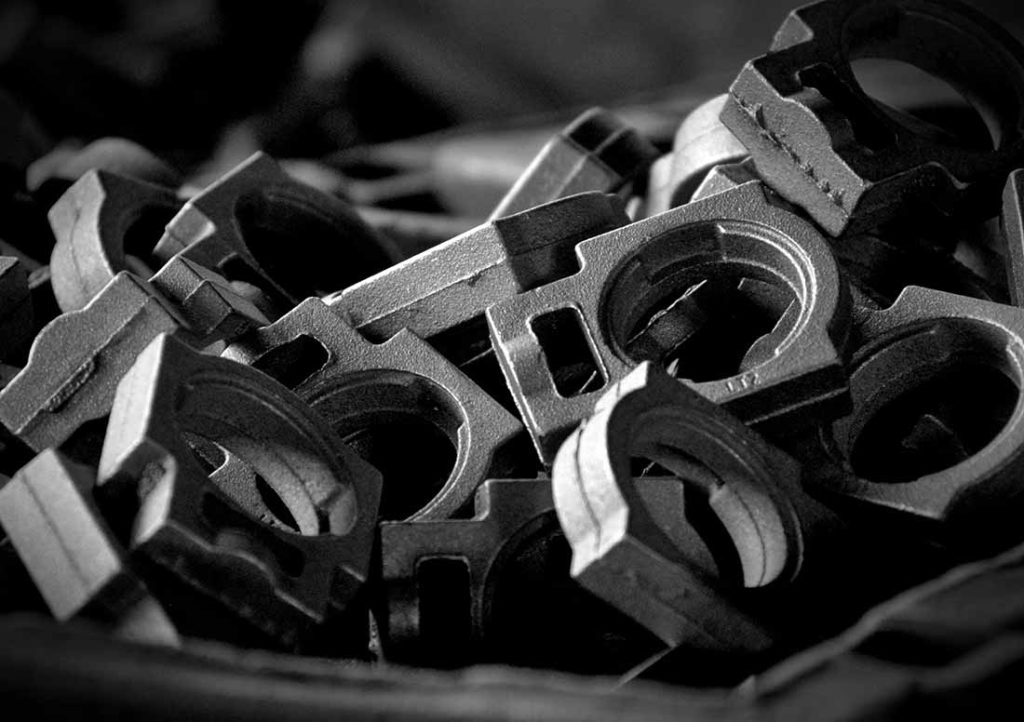
Precipitation-hardening (PH): فولادهای ضد زنگ رسوب سخت
فولادهای زنگ نزن سختکننده رسوبی (PH) خانوادهای از آلیاژهای مقاوم در برابر خوردگی هستند که برخی از آنها میتوانند برای ایجاد استحکام کششی 850 مگاپاسکال تا 1700 مگا پاسکال و استحکام تسلیم 520 مگاپاسکال تا بیش از 1500 مگاپاسکال – تقریباً سه یا چهار برابر فولاد آستنیتی بدون آستنیت، عملیات حرارتی شوند. مانند نوع 304 یا نوع 316. آنها در صنایع نفت و گاز، هسته ای و هوافضا استفاده می شوند که ترکیبی از استحکام بالا، مقاومت در برابر خوردگی و درجه چقرمگی به طور کلی کم اما قابل قبول است. سخت شدن رسوبی با افزودن مس، مولیبدن، آلومینیوم و تیتانیوم به صورت جداگانه یا ترکیبی حاصل می شود.
فولادهای ضد زنگ PH حاوی حدود 17 درصد کروم و 4 درصد نیکل هستند. عملیات حرارتی فولادهای PH را تا سطوحی بالاتر از آلیاژهای مارتنزیتی تقویت می کند. این فولادها با افزودن عناصری مانند مس، نیوبیم و آلومینیوم به فولاد می توانند استحکام بسیار بالایی داشته باشند.
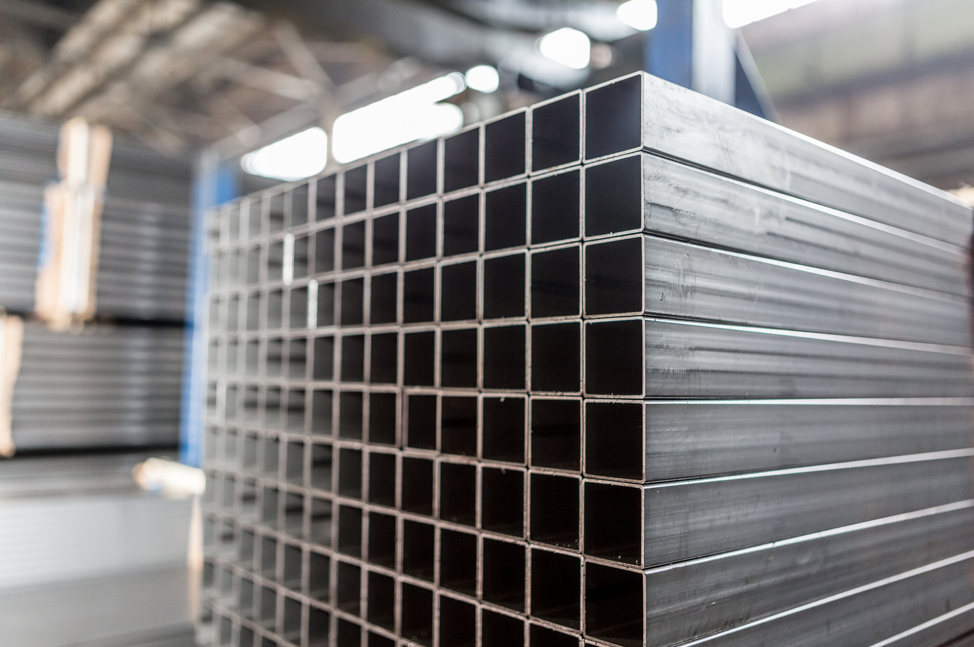
Duplex stainless steel: فولاد ضد زنگ دوبلکس
فولادهای ضدزنگ دوبلکس دارای ریزساختار مخلوطی از آستنیت و فریت هستند که نسبت ایده آل آن مخلوط 50:50 است، اگرچه آلیاژهای تجاری ممکن است نسبت 40:60 داشته باشند. آنها با کروم (19-32٪) و مولیبدن (تا 5٪) بیشتر و میزان نیکل کمتر نسبت به فولادهای زنگ نزن آستنیتی مشخص می شوند. فولادهای زنگ نزن دوبلکس تقریباً دو برابر فولاد زنگ نزن آستنیتی استحکام تسلیم دارند. ریزساختار مخلوط آنها مقاومت بهتری در برابر ترک خوردگی تنش کلریدی در مقایسه با فولاد زنگ نزن آستنیتی تیپ 304 و 316 ارائه می دهد. گریدهای دوبلکس بر اساس مقاومت در برابر خوردگی به سه زیر گروه تقسیم می شوند: دوبلکس ناب، دوبلکس استاندارد و سوپر دوبلکس.
خواص فولادهای زنگ نزن دوبلکس با محتوای آلیاژی کمتری نسبت به گریدهای فوق آستنیتی با عملکرد مشابه حاصل می شود و استفاده از آنها را برای بسیاری از کاربردها مقرون به صرفه می کند. صنعت خمیر و کاغذ یکی از اولین صنایعی بود که به طور گسترده از فولاد ضد زنگ دوبلکس استفاده کرد. امروزه صنعت نفت و گاز بزرگترین مصرف کننده است و برای گریدهای مقاوم در برابر خوردگی بیشتر تلاش کرده است که منجر به توسعه گریدهای سوپر دوبلکس و هایپر دوپلکس شده است. اخیراً، دوبلکس ناب ارزانتر (و کمی مقاومتر در برابر خوردگی) عمدتاً برای کاربردهای سازهای در ساختمانسازی و ساختوساز (میلههای تقویتکننده بتنی، صفحات برای پلها، کارهای ساحلی) و در صنعت آب توسعه یافته است.
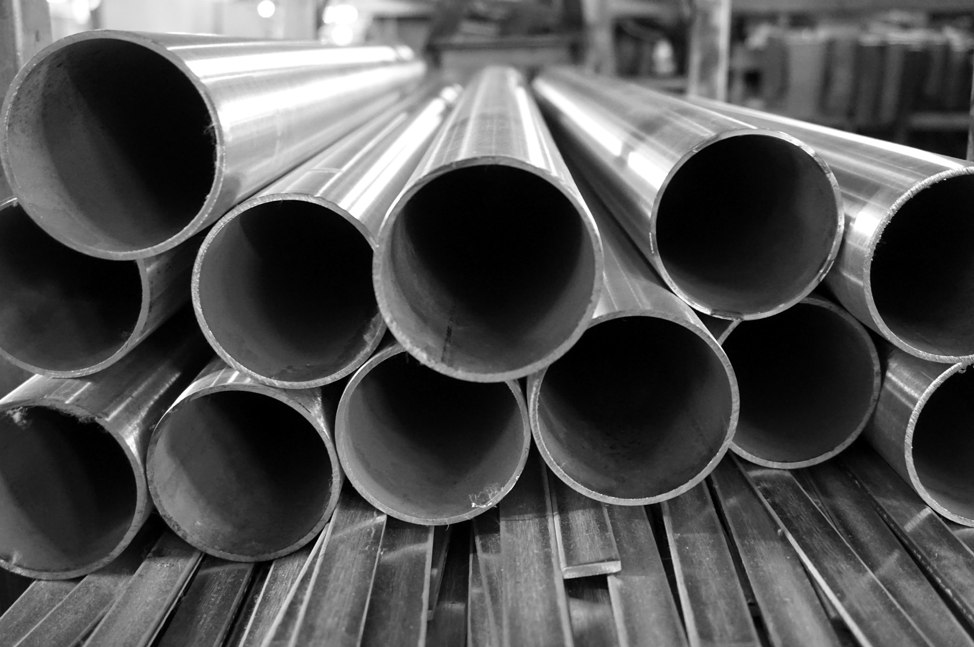
روش تولید
تولید فولاد ضد زنگ شامل یک سری فرآیندهای خاص می باشد که به ترتیب عبارت هستد از:
الف) ذوب شدن : فرآیند تولید شامل ذوب مواد خام در کوره قوس الکتریکی بین 8 تا 12 ساعت است. حرارت دادن مواد خام تا زمانی که فلز مذاب شود ادامه پیدا می کند.
ب) حذف محتوای کربن: محتوای کربن اضافی باید حذف شود. این کار را می توان با پردازش فلز مذاب در یک مبدل AOD (آرگون زدایی اکسیژن) انجام داد. استفاده از AOD با تزریق یک مخلوط اکسیژن-آرگون به کاهش کربن کمک می کند. عناصر آلیاژی مانند نیکل و مولیبدن را می توان به مبدل AOD اضافه کرد. هنگامی که به محصول کم کربن نیاز است، می توان از مبدل جایگزین VOD (کربورزدایی اکسیژن در خلاء) استفاده کرد.
ج) تنظیم : برای ایجاد تنظیمات در ترکیب شیمیایی، فرآیند تنظیم در روند تولید انجام می شود. در این فرآیند، فولاد برای حذف عناصر ناخواسته و افزایش قوام و در عین حال حفظ ترکیب مورد نیاز در محدوده دمایی، هم زده می شود.
د) تشکیل: فولاد مذاب به فرم هایی ریخته می شود. این فرم ها می توانند به شکل مستطیل، گرد یا مربع، دال، میله یا لوله باشند.
ه) نورد گرم: نورد گرم در دمایی بالاتر از دمای تبلور مجدد فولاد رخ می دهد. دمای دقیق بستگی به درجه فولاد ضد زنگ مورد نظر دارد. اسلب ها به صورت صفحه، نوار و ورق شکل می گیرند.
و) نورد سرد: این فرآیند زمانی استفاده می شود که به ابعاد خاص استثنایی نیاز باشد. در زیر دمای تبلور مجدد فولاد رخ می دهد. نورد سرد با استفاده از رول های با قطر کوچک و یک سری رول های نگهدارنده انجام می شود. این فرآیند امکان تولید ورق های عریض با پوشش سطحی بهبود یافته را فراهم می کند.
ه) آنیلینگ: بازپخت فرآیندی است که برای نرم کردن فولاد ضد زنگ، افزایش شکل پذیری و اصلاح ساختار دانه استفاده می شود. فولاد در این فرآیند تحت شرایط کنترل شده گرم و سرد می شود
و) رسوب زدایی: فرآیند بازپخت باعث ایجاد رسوب بر روی فولاد می شود. این رسوب ها معمولاً با استفاده از اسید برداشته میشوند که شامل حمام کردن فولاد در اسید نیتریک-هیدروفلوریک است. تمیز کردن الکتریکی یک روش جایگزین است که از جریان الکتریکی برای برداشتن جرم استفاده می کند.
ز) برش: فرآیند برش به برش فولاد ضد زنگ به اندازه دلخواه کمک می کند. فولاد ضد زنگ را می توان با چاقوهای گیوتینی برش داد، با استفاده از چاقوهای دایره ای، دایره ای برش داد، با استفاده از تیغه های پرسرعت اره کرد، یا با پانچ ها و قالب ها خالی کرد. روشهای دیگر عبارتند از برش با شعله، که از یک مشعل آتشسوزی با اکسیژن، پروپان و پودر آهن استفاده میکند، یا برش پلاسما جت که از یک ستون گاز یونیزه شده همراه با قوس الکتریکی برای برش فلز استفاده میکند.
ح) اتمام: پرداخت سطح به ارائه بهترین ظاهر به محصولات ضد زنگ کمک می کند. برای سنگ زنی یا صیقل دادن فولاد، از چرخ های سنگ زنی یا تسمه های ساینده استفاده می شود. روش های دیگر عبارتند از صاف کردن با چرخ های پارچه ای با ذرات ساینده، اچ خشک با استفاده از سندبلاست، و اچ مرطوب با استفاده از محلول های اسیدی است. نکته مهم این است که یک سطح صاف مقاومت در برابر خوردگی بهتری ایجاد می کند.
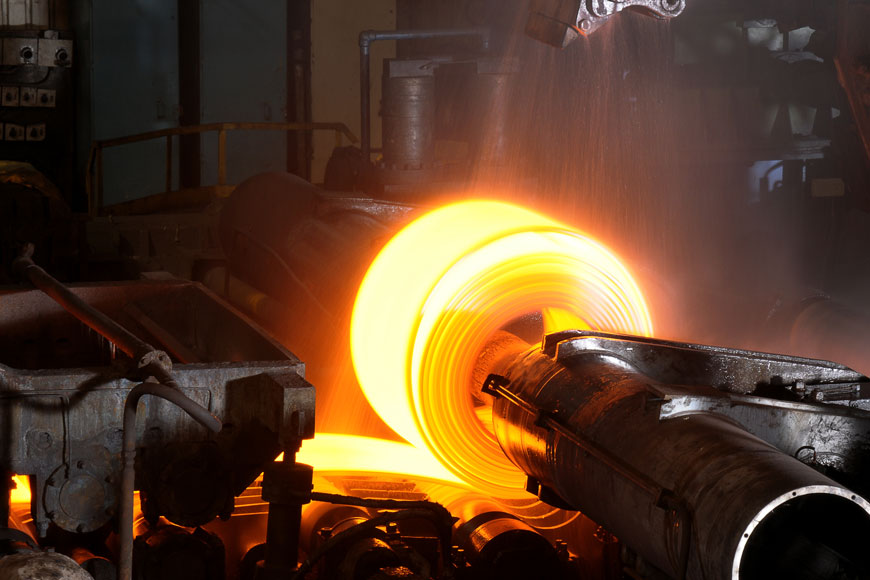
سخن پایانی
آشنایی با گرید ها و انواع فولاد ضد زنگ هنگام خریداری و مطابقت با نیاز های پروژه های خاص، بخش مهمی از تضمین نتایج طولانی مدت و بهینه سازی هزینه ها است. چه به دنبال فولادی مقاوم در برابر خوردگی برای محیط های مرطوب باشید یا برای تولید محصولات خود به یک ماده خیره کننده و براق ضدزنگ احتیاج دارید، همواره یکی از آلیاژهای فولاد ضد زنگ متناسب با نیاز شما در دسترس است. امروزه روش های تولید جدید فولاد ضد زنگ به ما این امکان را می دهد که به ضخامت ها و تحمل هایی برسیم که هیچ کس در زمان اختراع آن تصور نمی کرد. توانایی رسیدن به ضخامتهایی به کوچکی 0.00039 اینچ (بله 3 صفر صحیح است) کاتالیزوری در پیشبرد صنایع ساخت و ساز، حملونقل و پزشکی در آینده است که در نظر گرفتن ویژگی های دقیق به ما امکان می دهد خواص فیزیکی و استحکام آلیاژ نورد شده را افزایش دهیم.
شما میتوانید برای مشاوره خرید انواع فولاد ضد زنگ و فولاد آلیاژی برای پروژه های خود و دریافت قیمت روز با شماره 02158336، شرکت آرمان گستر اقتدار (آهن آرمان) تماس بگیرید تا کارشناسان ما، پاسخگوی سوالات شما باشند.